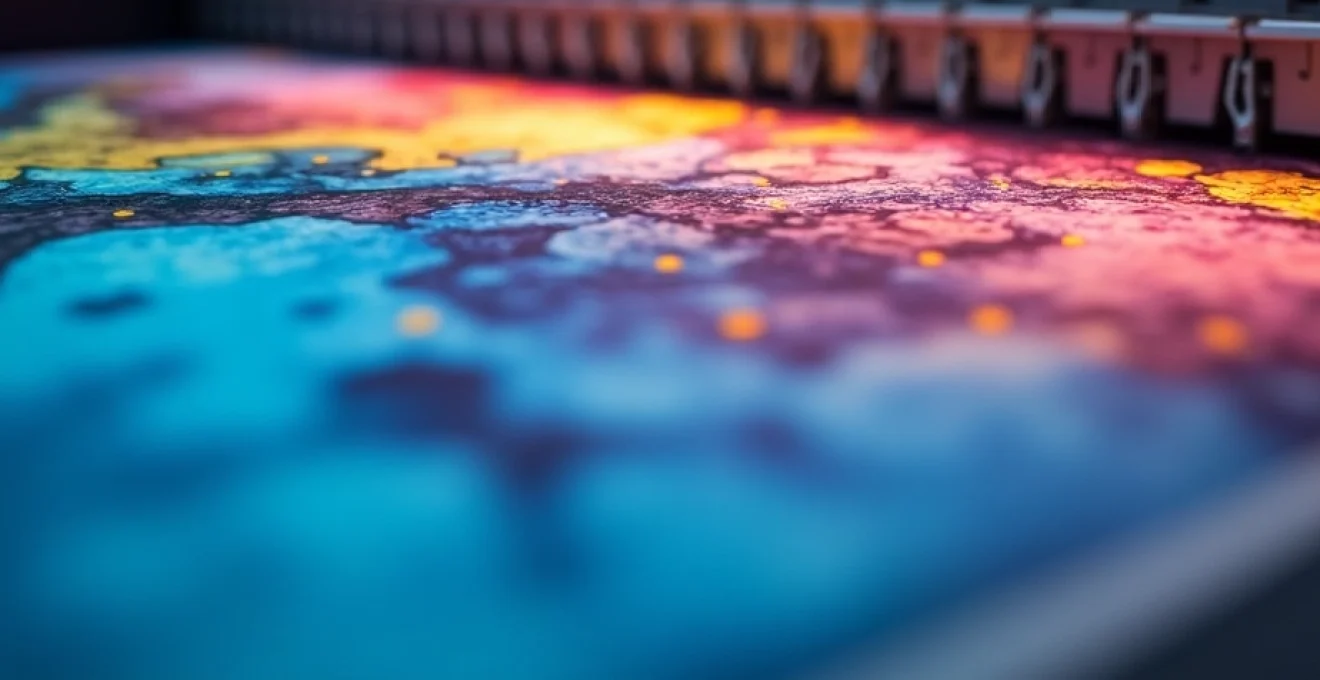
In today's fast-paced business environment, the demand for high-speed and accurate printing has never been greater. Professional printing machines have evolved to meet these stringent requirements, incorporating cutting-edge technologies that ensure rapid output without compromising on quality. From digital presses to industrial-grade printers, these sophisticated devices are revolutionizing the printing industry, offering unparalleled efficiency and precision that can make a significant difference in productivity and customer satisfaction.
High-speed printing technologies in professional machines
The cornerstone of modern professional printing is the ability to produce large volumes of printed material in record time. This capability is driven by a combination of advanced hardware and innovative software solutions. High-speed printing technologies have made it possible for businesses to meet tight deadlines and handle large-scale print jobs with ease.
One of the key factors contributing to increased printing speeds is the development of continuous-feed digital presses. These machines can print at speeds of up to 1,000 feet per minute, allowing for the production of thousands of pages in a single hour. This level of output was once the exclusive domain of offset printing, but digital technology has now caught up and, in many cases, surpassed traditional methods.
Another significant advancement is the implementation of single-pass printing technology. Unlike traditional printers that require multiple passes to apply different colors, single-pass printers can lay down all colors simultaneously, dramatically reducing printing time. This technology is particularly beneficial for large format printing and packaging applications where speed is crucial.
Advanced alignment systems
Precision in high-speed printing is not just about raw speed; it's also about maintaining accuracy at those high velocities. Advanced alignment systems play a crucial role in ensuring that each page is printed correctly, regardless of the printing speed. Two notable systems in this arena are Xerox FreeFlow and Canon PRISMAsync.
Xerox FreeFlow is a suite of software solutions that optimizes the entire print production process. It includes features like automated job scheduling and real-time production monitoring, which help maintain high accuracy even at top speeds. The system's intelligent workflow automation reduces manual intervention, minimizing errors and ensuring consistent output quality.
Similarly, Canon's PRISMAsync is a digital front end (DFE) system that offers sophisticated color management and precise paper handling. It uses a unique color control loop that continuously monitors and adjusts color output, ensuring accuracy even during long print runs. PRISMAsync also features intelligent queue management, which helps optimize the printing order to maximize efficiency without sacrificing quality.
Microfluidic ink delivery
The way ink is delivered to the printing surface has a significant impact on both speed and accuracy. Two leading technologies in this field are HP's Thermal Inkjet and Epson's PrecisionCore.
HP's Thermal Inkjet technology uses heat to eject ink droplets onto the paper. This method allows for very precise control over droplet size and placement, resulting in sharp, clear prints. The technology is capable of ejecting droplets at a rate of up to 36,000 per second, contributing to high-speed printing capabilities.
In contrast, Epson's PrecisionCore technology uses piezoelectric crystals to eject ink droplets. This mechanical process allows for even finer control over droplet size and can operate at extremely high frequencies. PrecisionCore printheads can fire up to 50,000 droplets per second, enabling both high speed and high resolution printing.
Both technologies have their strengths, and the choice between them often depends on specific application requirements. HP's Thermal Inkjet is known for its reliability and consistency, while Epson's PrecisionCore is praised for its versatility and ability to handle a wide range of ink types.
Calibration techniques
Maintaining color accuracy and consistency is crucial in professional printing, especially when operating at high speeds. Advanced calibration techniques and tools are essential for ensuring that every print meets the required color standards. Two leading solutions in this field are the X-Rite i1Pro 3 and the Konica Minolta FD-9.
The X-Rite i1Pro 3 is a spectrophotometer that offers high-speed measurements for a wide range of materials and surfaces. It can measure M0, M1, and M2 simultaneously, providing a comprehensive color profile in a single pass. This device is particularly useful for calibrating monitors, printers, and proofing devices, ensuring color consistency across different media and output devices.
The Konica Minolta FD-9 is an auto-scan spectrophotometer designed for high-volume color measurements. It can measure up to 1,500 color patches in approximately 1 minute, making it ideal for creating and verifying color profiles for high-speed printing systems. The FD-9's ability to quickly measure large color charts helps maintain color accuracy even during long print runs.
Precision engineering for accurate print output
While speed is crucial in professional printing, it must be balanced with precision to ensure high-quality output. Precision engineering in modern printing machines focuses on maintaining accuracy at high speeds through a combination of mechanical design, electronic controls, and software algorithms.
One key aspect of precision engineering in printing is registration control . This refers to the alignment of different color layers or front and back sides of a sheet. Advanced registration systems use high-speed cameras and sophisticated image processing algorithms to detect and correct misalignments in real-time, ensuring that each element of the print is precisely positioned.
Another critical factor is paper handling . Professional printing machines employ advanced paper transport systems that can move sheets at high speeds while maintaining tight control over their position. These systems often use air-assisted feeding and vacuum belts to prevent paper jams and ensure smooth movement through the printer.
Precision in printing is not just about the final output; it's about controlling every variable in the process to achieve consistent, repeatable results.
The integration of closed-loop control systems is another hallmark of precision engineering in professional printing machines. These systems continuously monitor various parameters such as temperature, humidity, and ink density, making real-time adjustments to maintain optimal printing conditions. This level of control is essential for achieving consistent quality across long print runs.
Industrial-grade components for reliability and speed
The backbone of any high-speed, accurate printing system is its hardware. Professional printing machines are built with industrial-grade components designed to withstand the rigors of continuous operation while maintaining precision. These components are engineered to tighter tolerances and are made from more durable materials than their consumer-grade counterparts.
One critical area where industrial-grade components make a significant difference is in the print heads . Professional printers often use print heads with a higher nozzle count and more precise droplet control. For example, some high-end print heads can produce droplets as small as 1.2 picoliters, allowing for extremely fine detail and smooth color transitions.
High-capacity paper handling
Efficient paper handling is crucial for maintaining high printing speeds without compromising accuracy. The Ricoh IM C8000 Series exemplifies the use of industrial-grade components in paper handling systems. This series features a high-capacity paper tray that can hold up to 8,100 sheets, minimizing the need for frequent reloading during large print jobs.
The IM C8000 Series also incorporates advanced paper feed technology that can handle a wide range of paper weights and sizes. Its air-assisted paper separation and vacuum feed system ensure reliable feeding even at high speeds, reducing the risk of paper jams and misfeeds that can disrupt production.
Robust print engines
The heart of any professional printing machine is its print engine. Two examples of robust, industrial-grade print engines are the Fuji Xerox Iridesse and the Kodak NexPress Platform.
The Fuji Xerox Iridesse is known for its ability to print with up to six colors in a single pass, including specialty metallic and clear inks. Its print engine is designed for high-volume production, capable of printing up to 120 pages per minute at 2400 x 2400 dpi resolution. The Iridesse uses advanced EA-Eco LGK toner and an innovative imaging system to achieve exceptional print quality even at high speeds.
The Kodak NexPress Platform is another example of industrial-strength printing technology. It features a modular design that allows for easy upgrades and maintenance, ensuring long-term reliability. The NexPress can handle a wide range of substrates and offers a fifth imaging unit for applying specialty inks or coatings. Its robust construction and advanced thermal imaging technology enable it to maintain consistent quality over long print runs.
Advanced cooling systems
Maintaining optimal operating temperatures is crucial for ensuring consistent print quality and longevity of components in high-speed printing machines. The Heidelberg Speedmaster XL 106 showcases advanced cooling technology that addresses this challenge effectively.
The Speedmaster XL 106 employs a sophisticated temperature control system that regulates the temperature of key components such as the inking units, dampening system, and impression cylinders. This system uses a combination of water and air cooling to maintain stable temperatures even during high-speed operation.
One notable feature is the AirTransfer system, which uses a cushion of air to transport sheets through the press without contact. This not only prevents heat buildup on the sheets but also contributes to precise registration and reduced risk of marking. The press also incorporates intelligent energy management systems that optimize power consumption while ensuring all components operate at their ideal temperatures.
Digital front end (DFE) systems for efficient workflow
Digital Front End (DFE) systems are the brains behind modern professional printing machines, orchestrating the entire printing process from file input to final output. These sophisticated software solutions play a crucial role in maintaining both speed and accuracy in high-volume printing operations.
DFE systems handle a wide range of tasks, including job queuing, color management, imposition, and print quality optimization. They act as the interface between the design software and the printing hardware, ensuring that what you see on the screen is accurately reproduced on paper.
RIP processing
At the core of any DFE system is the Raster Image Processor (RIP), which converts digital files into the bitmap images that the printer can understand. Two leading RIP technologies in the professional printing world are Adobe APPE (Adobe PDF Print Engine) and EFI's Fiery FS400 Pro.
Adobe APPE is designed to handle complex PDF files with efficiency and accuracy. It processes PDF files natively, without conversion to intermediate formats, which helps maintain the integrity of the original design. APPE is particularly adept at handling transparency and layers, ensuring that complex designs are rendered correctly.
Fiery FS400 Pro, on the other hand, is known for its speed and versatility. It can process multiple jobs simultaneously and offers advanced color management features. The Fiery system also includes powerful preflight and error correction tools, which help catch and resolve potential issues before they reach the printer.
Cloud integration
Cloud integration has become a crucial feature in modern DFE systems, allowing for greater flexibility and efficiency in print workflow management. Two notable examples of cloud-integrated DFE systems are Xerox FreeFlow Core and HP PrintOS.
Xerox FreeFlow Core is a browser-based solution that automates and integrates the steps in the print production process. It allows users to create workflows that can be accessed and managed from anywhere, improving collaboration and reducing turnaround times. FreeFlow Core can also integrate with third-party software, making it a versatile solution for diverse printing environments.
HP PrintOS is a cloud-based print production operating system that offers a suite of web and mobile apps to help print operations run more efficiently. It provides real-time visibility into the production environment, allowing managers to make data-driven decisions. PrintOS also includes features like automated job submission and remote monitoring, which contribute to increased productivity and reduced downtime.
Variable data printing
Variable Data Printing (VDP) is a critical capability for many professional printing applications, allowing for personalized content in high-volume print runs. Two leading solutions in this space are XMPie uDirect and Objectif Lune PlanetPress.
XMPie uDirect is a powerful VDP solution that integrates seamlessly with Adobe Creative Suite. It allows designers to create dynamic content using familiar tools, then links this content to databases for personalization. uDirect supports a wide range of data formats and can handle complex logic for creating highly targeted, personalized print materials.
Objectif Lune PlanetPress is another robust VDP solution, known for its flexibility and scalability. It can handle both transactional and promotional printing needs, making it suitable for a wide range of applications. PlanetPress includes features for data cleansing and enrichment, ensuring that the variable data used in printing is accurate and effective.
Quality assurance technologies in professional printing
Maintaining consistent quality in high-speed printing environments is a significant challenge. Professional printing machines incorporate a range of quality assurance technologies to ensure that every print meets the required standards, even when producing thousands of pages per hour.
These technologies work in real-time, continuously monitoring and adjusting various parameters to maintain optimal print quality. They cover aspects such as color accuracy, registration, and print defect detection, providing a comprehensive approach to quality control.
In-line spectrophotometry
In-line spectrophotometry is a crucial technology for maintaining color accuracy and consistency in high-speed printing. Two notable systems in this field are the Konica Minolta IQ-501 and the Screen TruePress.
The Konica Minolta IQ-501 is an intelligent quality optimizer that uses in-line spectrophotometry to continuously monitor and adjust color and registration. It can perform these adjustments in real-time, without stopping the press, ensuring consistent quality throughout the print run. The IQ-501 can also automate many calibration and setup processes, reducing makeready time and minimizing operator intervention.
The Screen TruePress incorporates a similar in-line color management system. It uses a spectrophotometer to measure color patches printed alongside the main job, making continuous adjustments to maintain color accuracy. This system is particularly effective for ensuring consistency across long print runs and between different jobs.
Automated defect detection
Detecting and correcting print defects in real-time is essential for maintaining quality in high-speed printing operations. Two leading systems in this area are the AVT Helios and QuadTech Inspection Systems.
The AVT Helios is a comprehensive print inspection system that uses high-resolution cameras and advanced image processing algorithms to detect a wide range of print defects. It can identify issues such as color variations, registration errors, and print clarity problems in real-time, allowing for immediate correction. The system can be customized to focus on specific areas of concern for different print applications.
QuadTech Inspection Systems offer similar capabilities, with a focus on web offset and gravure printing. These systems use high-speed cameras and sophisticated software to compare each printed page against a "golden template," identifying any deviations. QuadTech systems can detect issues as small as missing periods in text, ensuring that even minute defects are caught and corrected.
Color management
Effective color management is crucial for achieving consistent, accurate color reproduction across different printing devices and substrates. Two leading solutions in this field are GMG ColorServer and Esko Color Engine.
GMG ColorServer is a powerful color management solution that automates the process of converting colors between different color spaces and output devices. It ensures that colors are reproduced consistently, regardless of the printing technology or substrate used. GMG ColorServer is particularly useful in environments where the same job may be printed on multiple devices or where color accuracy is critical.
Esko Color Engine is another sophisticated color management tool, designed to ensure color consistency across the entire packaging and label production workflow. It offers features such as ink saving, gamut mapping, and support for extended gamut printing. It integrates with packaging-specific design tools and can handle a wide range of packaging-specific color requirements, including spot colors and special inks.
Both GMG ColorServer and Esko Color Engine play crucial roles in ensuring that the high speed and accuracy of modern printing machines translate into consistent, high-quality color output. They help bridge the gap between design intent and printed reality, a critical factor in maintaining customer satisfaction and brand consistency.