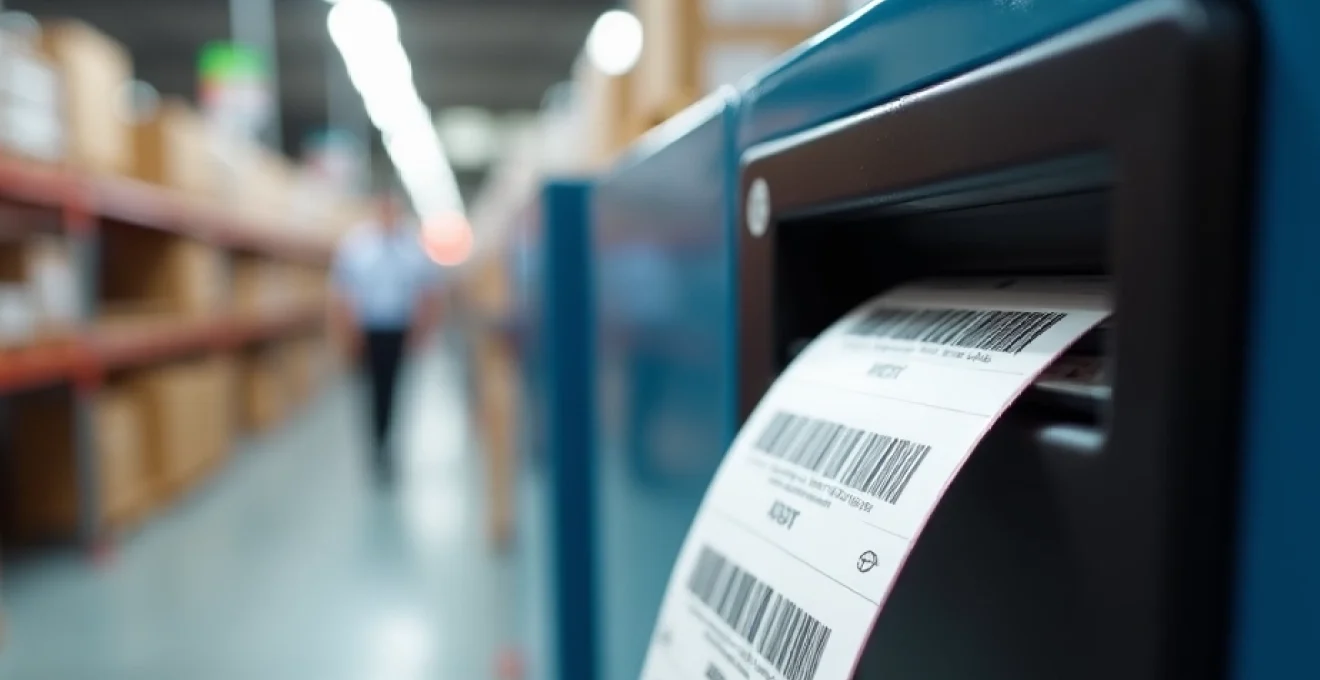
In today's environmentally conscious business landscape, companies are constantly seeking innovative ways to reduce waste and enhance operational efficiency. Linerless printers have emerged as a game-changing solution, offering significant benefits in waste reduction and process optimization. These cutting-edge devices are revolutionizing label printing across various industries, from retail to logistics, by eliminating the need for traditional liner-backed labels.
Linerless printing technology addresses two critical challenges faced by businesses: environmental sustainability and operational productivity. By removing the backing liner from labels, these printers substantially decrease waste generation while simultaneously streamlining printing processes. This dual advantage makes linerless printers an attractive option for companies looking to minimize their ecological footprint without compromising on performance.
Linerless printer technology: core mechanisms and innovations
At the heart of linerless printing technology lies a sophisticated system that fundamentally alters the way labels are produced and applied. Unlike traditional printers that rely on pre-cut labels with a disposable backing, linerless printers utilize a continuous roll of adhesive-backed material. This innovation eliminates the need for a separate liner, resulting in a more compact and efficient printing solution.
The core mechanism of a linerless printer involves a specialized print head that directly applies ink or thermal transfer onto the adhesive-backed material. This process is complemented by an integrated cutting system that precisely cuts labels to the desired length, allowing for variable sizing and reducing material waste. The absence of a liner also necessitates the use of a non-stick platen roller, which prevents the adhesive from sticking to the printer's internal components.
One of the key innovations in linerless printing is the development of advanced adhesive formulations. These adhesives are designed to maintain their tackiness while remaining inert until application, ensuring that the labels do not stick to each other on the roll. This delicate balance is achieved through careful chemical engineering and has been a significant factor in the widespread adoption of linerless technology.
To fully grasp the potential of this technology, click here to learn more about the specifics of thermal linerless printers and their applications in various industries.
Waste reduction through adhesive-backed media
The most significant environmental benefit of linerless printers is the substantial reduction in waste material. Traditional label printing generates a considerable amount of waste in the form of discarded backing liners. These liners, typically made of silicone-coated paper or plastic, are not easily recyclable and often end up in landfills. By eliminating this backing, linerless printers can reduce label-related waste by up to 40%.
Direct thermal linerless labels: composition and properties
Direct thermal linerless labels are composed of a single layer of thermosensitive material with an adhesive backing. The thermosensitive layer contains chemicals that change color when exposed to heat, allowing for printing without the need for ink or ribbons. This composition not only reduces waste but also simplifies the printing process, as there are fewer consumables to manage.
Silicone coating technology for release properties
To prevent linerless labels from sticking to each other on the roll, a thin layer of silicone coating is applied to the non-adhesive side of the material. This coating acts as a release agent, allowing the labels to separate easily without damaging the adhesive or the printed surface. The silicone coating technology has been refined over the years to provide optimal release properties while maintaining print quality and adhesion strength.
Adhesive pattern optimization for minimal residue
Linerless label manufacturers have developed sophisticated adhesive patterns that minimize residue and improve application efficiency. These patterns often feature small gaps or channels in the adhesive layer, which allow air to escape during application, reducing the formation of bubbles and ensuring a smooth, secure attachment. This optimization not only enhances the label's performance but also contributes to waste reduction by minimizing the need for reapplication due to poor adhesion.
Comparison with traditional liner-based labels
When compared to traditional liner-based labels, linerless alternatives offer several advantages in terms of waste reduction:
- Elimination of backing liner waste
- Reduced packaging material for label rolls
- Lower transportation costs and emissions due to decreased weight and volume
- Simplified recycling process for used labels
- Decreased storage space requirements for label inventory
These benefits collectively contribute to a significant reduction in the overall environmental impact of labeling operations, making linerless printers an eco-friendly choice for businesses across various sectors.
Efficiency gains in printing and application processes
Beyond waste reduction, linerless printers offer substantial efficiency improvements in both printing and application processes. These gains translate into increased productivity, reduced downtime, and lower operational costs for businesses adopting this technology.
Continuous roll feeding vs. sheet-fed systems
Linerless printers utilize a continuous roll feeding system, which offers several advantages over traditional sheet-fed printers:
- Uninterrupted printing for extended periods
- Reduced frequency of media changes
- Faster printing speeds due to continuous movement of media
- Elimination of paper jams associated with sheet feeding mechanisms
This continuous feeding system allows for higher throughput and less operator intervention, resulting in improved overall efficiency.
Auto-length adjustment and variable label sizing
One of the most significant efficiency gains offered by linerless printers is the ability to adjust label length on-the-fly. This feature, known as auto-length adjustment, allows for the printing of variable-sized labels from a single roll of media. The printer's integrated cutting mechanism precisely cuts each label to the required length, eliminating the need for pre-sized label stock and reducing inventory complexity.
Variable label sizing offers several benefits:
- Reduced material waste by printing only the required label size
- Increased flexibility in label design and information content
- Simplified inventory management with fewer stock keeping units (SKUs)
- Improved adaptability to changing labeling requirements
Integrated cutting mechanisms: guillotine vs. rotary
Linerless printers typically employ one of two types of integrated cutting mechanisms: guillotine or rotary cutters. Each type has its advantages:
Guillotine Cutter | Rotary Cutter |
---|---|
Clean, straight cuts | Higher cutting speed |
Suitable for thicker materials | Lower maintenance requirements |
Precise control over cut length | Continuous operation capability |
The choice between these cutting mechanisms depends on factors such as the specific application requirements, printing speed, and material characteristics.
Print head longevity and maintenance reduction
Linerless printers often feature advanced print head technologies that contribute to increased longevity and reduced maintenance requirements. The absence of a liner reduces friction and wear on the print head, leading to several benefits:
- Extended print head life
- Decreased frequency of print head replacements
- Reduced downtime for maintenance
- Lower overall operational costs
These factors combine to enhance the overall efficiency and reliability of linerless printing systems, making them an attractive option for businesses seeking to optimize their labeling operations.
Environmental impact and sustainability metrics
The adoption of linerless printing technology contributes significantly to environmental sustainability efforts. To quantify these benefits, businesses and researchers have developed various metrics and assessment tools. Some key sustainability metrics associated with linerless printing include:
- Reduction in carbon footprint (measured in CO2 equivalent)
- Decrease in landfill waste (measured in weight or volume)
- Energy savings in production and transportation
- Water conservation in manufacturing processes
- Reduction in use of non-renewable resources
Many companies have reported substantial improvements in these areas after switching to linerless printing solutions. For example, some businesses have achieved up to a 30% reduction in their labeling-related carbon footprint and a 40% decrease in landfill waste.
"The transition to linerless printing has allowed us to meet our sustainability goals while improving operational efficiency. It's a win-win for both the environment and our bottom line."
Furthermore, the use of linerless labels aligns with circular economy principles by reducing the overall material input and simplifying the recycling process for used labels. This alignment with sustainability objectives has made linerless printing an attractive option for companies looking to enhance their environmental credentials and appeal to eco-conscious consumers.
Integration with existing workflows and systems
One of the critical factors in the successful adoption of linerless printing technology is its ability to integrate seamlessly with existing workflows and systems. Many linerless printer manufacturers have developed solutions that are compatible with standard label design software, warehouse management systems (WMS), and enterprise resource planning (ERP) platforms.
The integration process typically involves several key steps:
- Assessment of current labeling requirements and processes
- Selection of appropriate linerless printer models and media
- Configuration of printer settings and software interfaces
- Training of staff on new equipment and procedures
- Gradual implementation and performance monitoring
Successful integration often requires collaboration between IT departments, operations teams, and equipment suppliers to ensure that the new linerless printing solution complements existing systems without disrupting critical business processes.
Many linerless printers support industry-standard connectivity options such as Ethernet, USB, and wireless interfaces, facilitating easy integration with networked environments. Additionally, some advanced models offer cloud connectivity and remote management capabilities, enabling centralized control and monitoring of printing operations across multiple locations.